
Gravity cast wheels
Gravity casting, a wheel manufacturing process on the verge of extinction, primarily involves filling the entire wheel mold with molten aluminum by its own weight and allowing it to solidify naturally. This method has a higher yield rate and lower mold cost; however, it also has obvious drawbacks. The difficulty lies in controlling the flow time of the liquid metal because during slow flow, there is inevitably a temperature difference between the far end from the pouring gate and other parts of the mold. Therefore, stable temperature control of the mold becomes crucial as both excessively high or low temperatures can affect the quality of wheel production. To prevent premature solidification, aluminum temperature needs to be increased but this may result in uneven molecular distribution and more sand holes forming. Consequently, to maintain strength, more molten aluminum must be poured into the mold which increases the weight of gravity cast wheels.
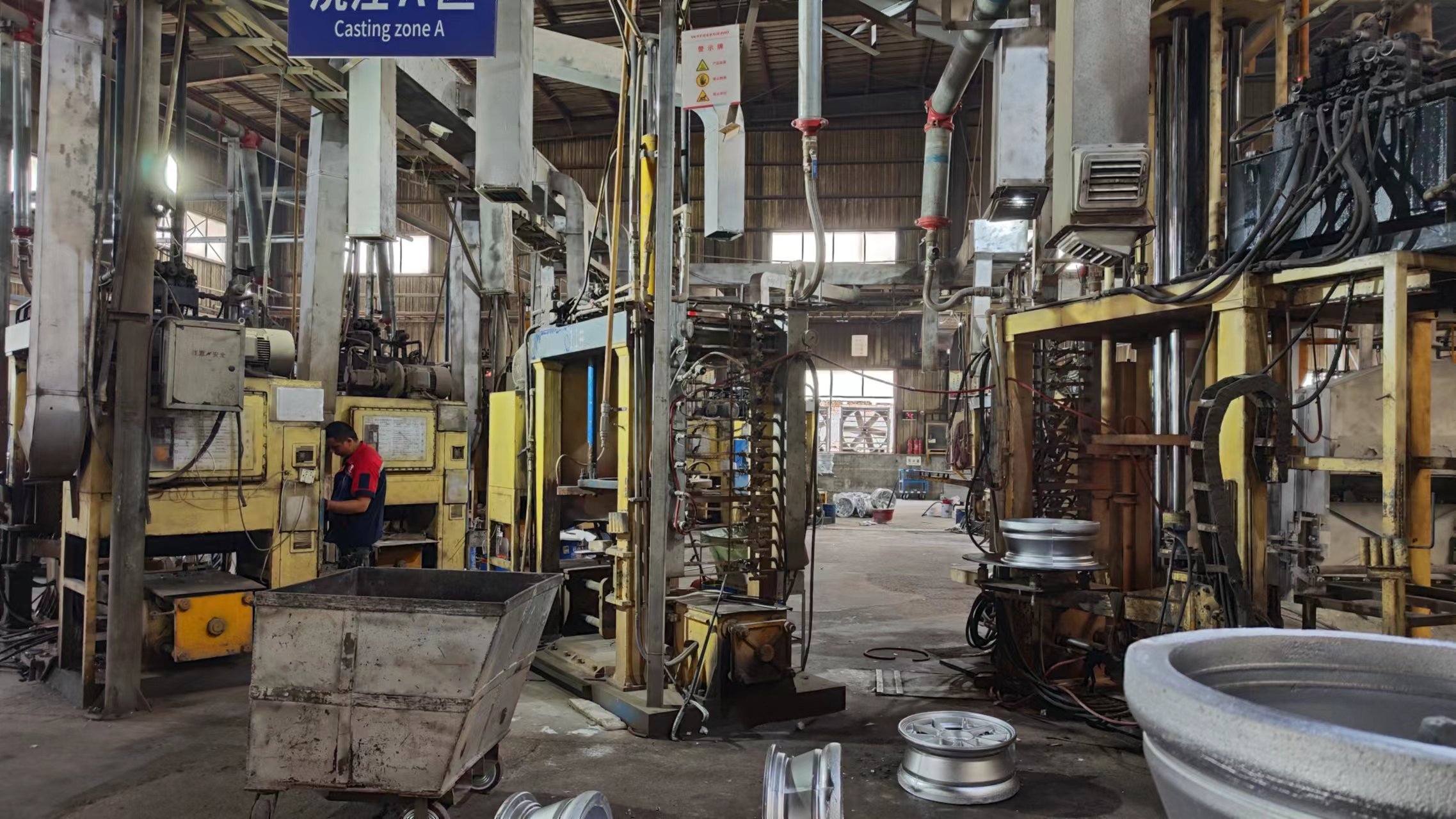
To improve the quality and stability of gravity cast wheels, we can implement some process improvements. For example, optimizing structural layout and increasing cooling channels in mold design can enhance material solidification uniformity; meticulous selection and treatment of raw materials ensure their purity and physical properties meet requirements; furthermore, post-processing steps such as heat treatment and machining can strengthen overall wheel strength. In conclusion, while gravity casting offers advantages such as simplicity, efficiency, and low cost, attention must be paid to its quality issues by taking appropriate measures to enhance product quality and reliability. Only by balancing production efficiency with product quality can we better meet market demands while ensuring users' safer driving experiences.
Gravity cast wheel diagram:
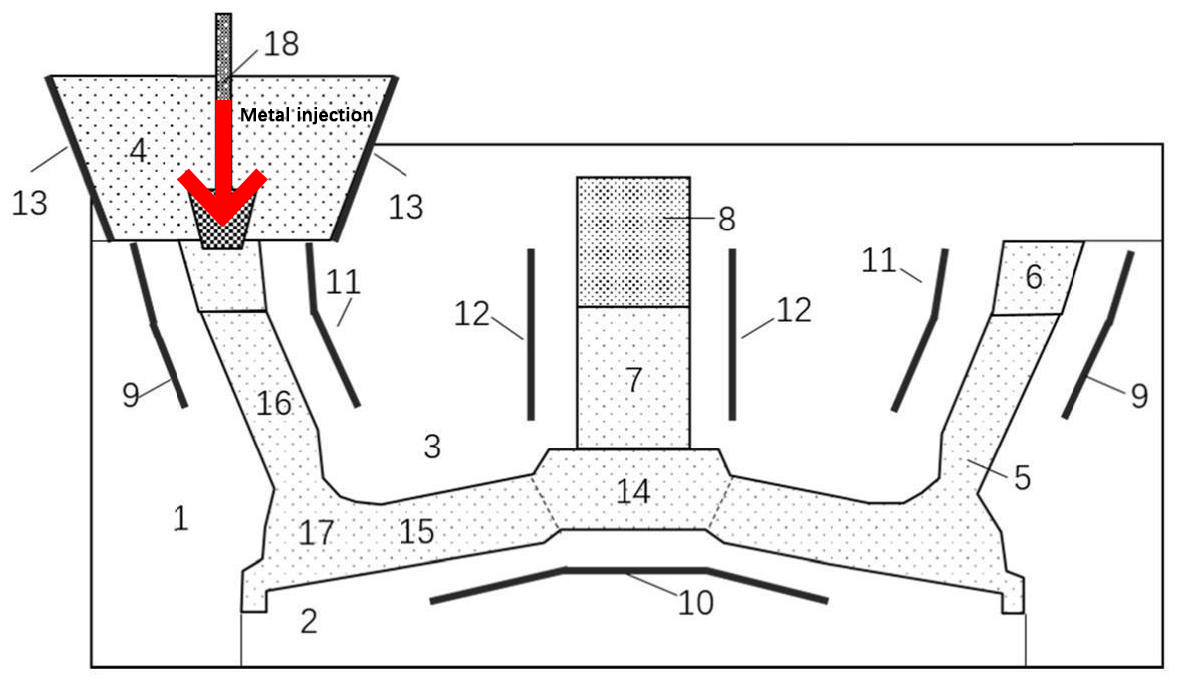