
low pressure casting wheel
The low-pressure casting method is not only about placing it above a sealed crucible and forming low pressure (0.06-0.15 MPa) on the surface of the molten metal by introducing compressed air, but also about filling the mold and controlling solidification as the metal liquid rises through the riser tube.
At the same time, it has the following characteristics: firstly, this casting method can achieve good feeding shrinkage. By controlling the flow velocity and direction of the metal liquid under low pressure, it can effectively fill the entire mold and avoid defects such as porosity and inclusions.
Although under the action of low pressure, the density of the wheel becomes higher, but the distance from the goal of lightweight is still a little short.
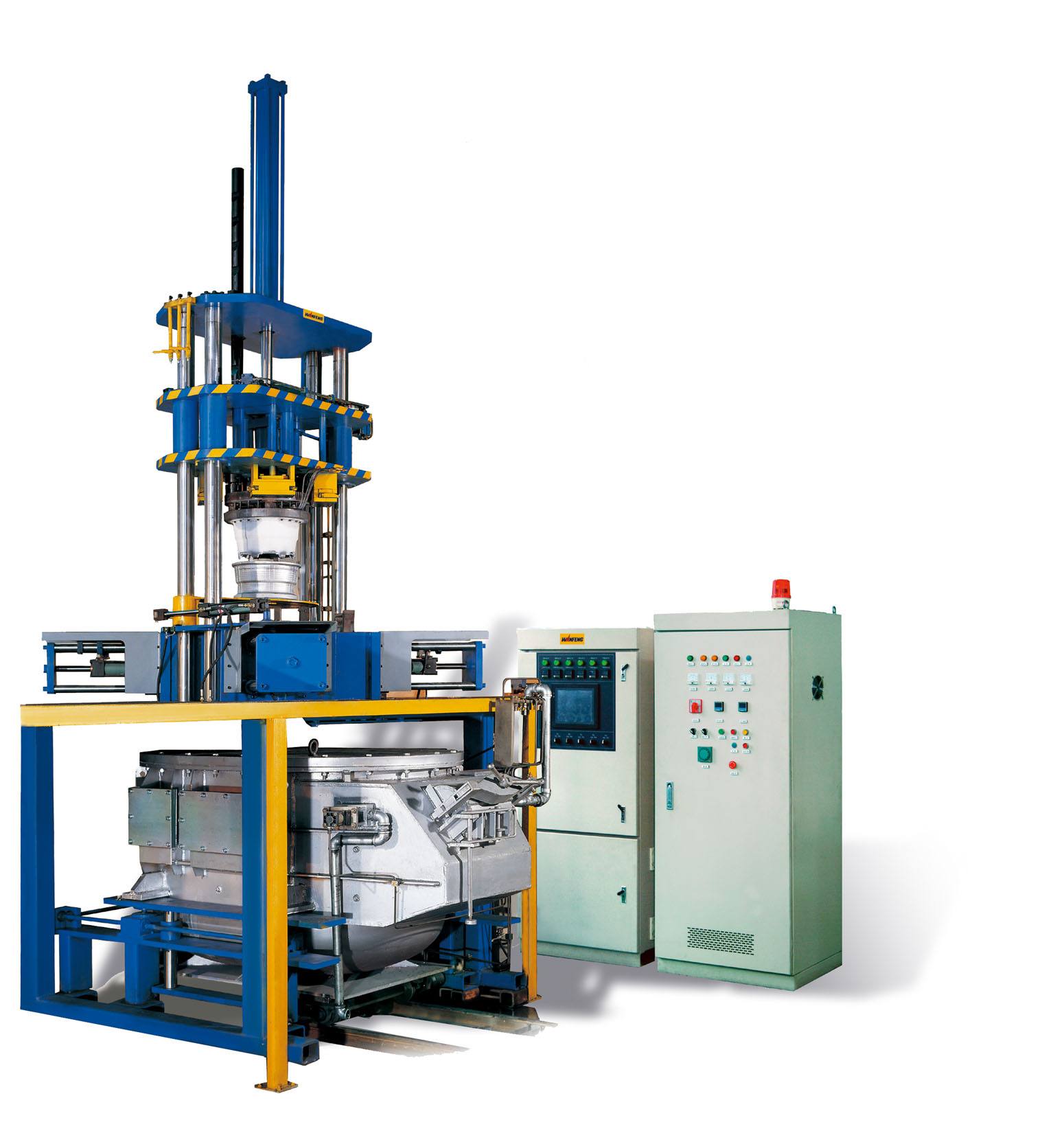
Secondly, compact hub structure is another significant feature of this casting method.
Due to minimal impact and squeezing force on the metal liquid during filling process, internal structure of hubs becomes more compact and uniform, improving strength and durability of parts. In addition, compared with traditional casting methods, no gating system is required for this method.
Traditional casting requires gating systems to remove gases and impurities generated in molten metals which increases complexity in processing steps.
However, using this method eliminates gate design and processing steps while greatly simplifying production processes.
Most importantly, when using this technology for casting purposes, high metal yield rate can be achieved at over 95%.
This is because precise control under low-pressure conditions allows minimal or even zero waste material after entering molds and solidifying.
Furthermore,this new technology is environmentally friendly with no pollution,and has high recycling efficiency which effectively saves resources.In conclusion,this novel automated casting method based on controlled solidification principles not only improves product quality ,production efficiency,and resource utilization,but also meets environmental requirements.It has broad prospects for application in modern industrial fields
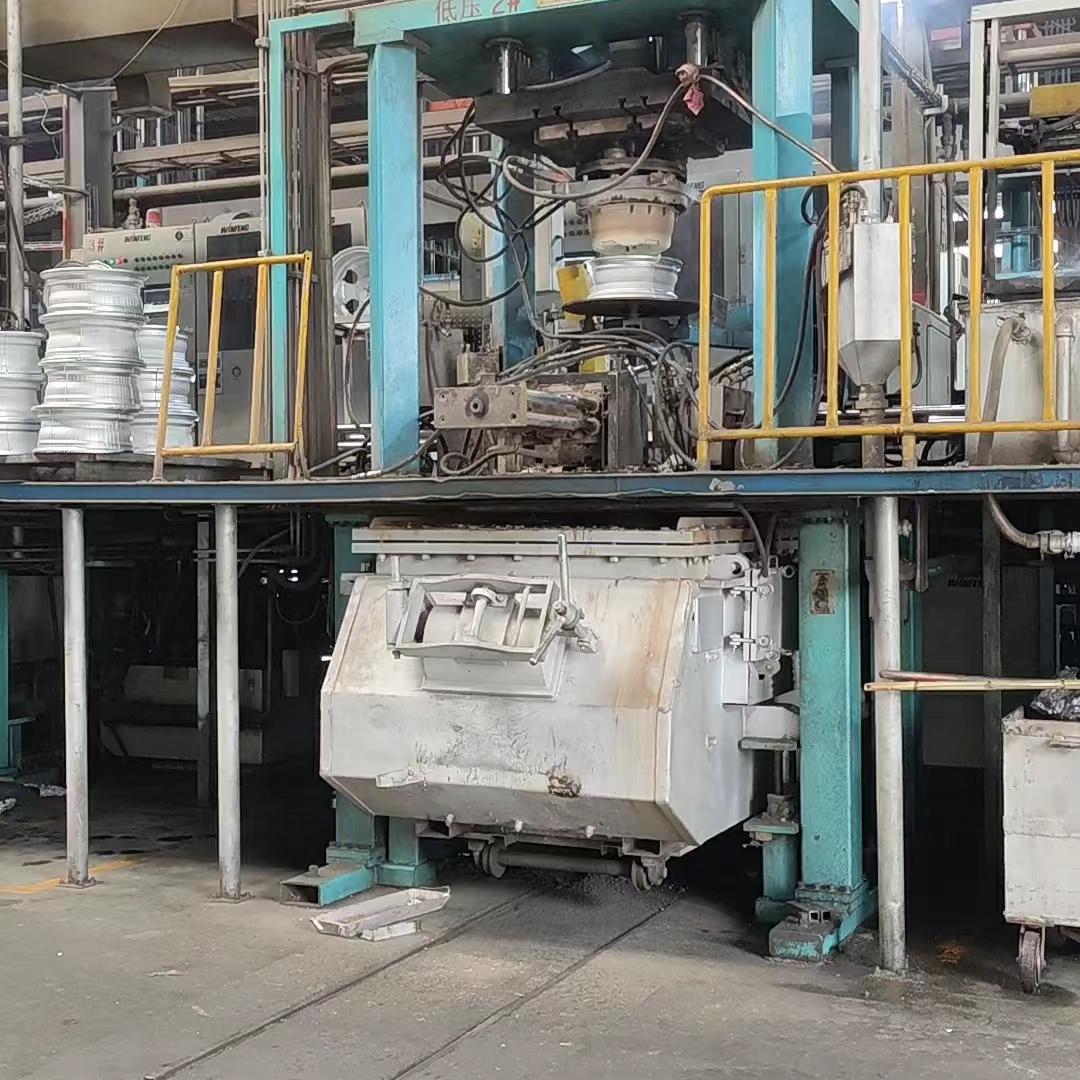